David Tibbetts, CSP
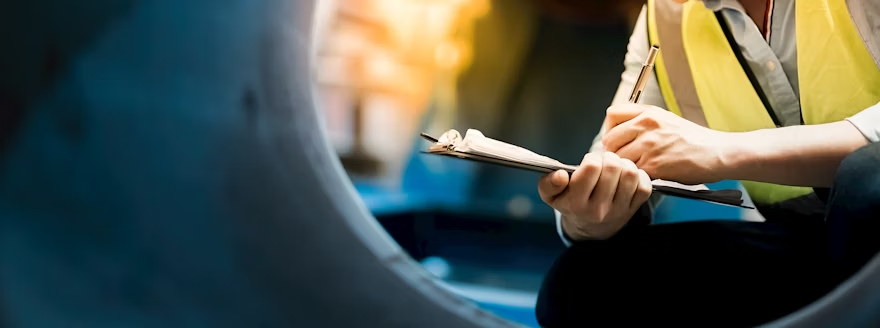
Would you refuse to hire an employee because they failed a course in college? Of course not. You would ask follow-up questions to understand why they failed, how they've changed their approach and how they are currently performing. The same principle applies to hiring a contractor.
Most contractor prequalification systems only consider lagging indicators, such as OSHA 300A forms; Experience Modification Ratings (EMR); Total Recordable Incident Rates (TRIR); and Days Away, Restricted Duty or Job Transfer (DART) case rates to determine a contractor's risk. While these factors are important, they do not tell the entire story.
Your project team also needs to evaluate leading indicators, including safety programs, management practices and culture, to gain a comprehensive understanding of risk. Research suggests that evaluating leading indicators can reduce construction injury rates. According to the study, companies with higher safety management system scores were less likely to have recordable incidents. However, many project teams don't collect this information. In a recent evaluation, safety management system elements were absent in 90% of industry safety prequalification surveys.
Relying solely on lagging indicators can lead project managers to disqualify capable contractors, especially when using a pass/fail rating system. With today's construction worker shortage, many companies are unnecessarily limiting their contractor pool, while also leaving themselves open to risk.
A comprehensive contractor evaluation process requires gathering the right data that provides an understanding of past performance but also creates a predictive view of safety risk. Considering these extra variables results in better project outcomes and contractor success.
The Problem with Lagging Indicators
Lagging indicators provide a limited, often oversimplified view of a contractor's safety performance. Recordable incidents, EMRs, DART rates and other historical metrics disclose past performance but are not necessarily indicative of future risk, which could result in misinterpretations and potentially unfair assessments of a contractor's current safety capabilities and culture.
Despite industry assumptions, a low TRIR is not directly related to operational safety. Just because something has not happened in the past does not mean it won't happen in the future. Additionally, recordable incident reporting treats all events equally, regardless of severity. Incidents can range from minor injuries like a cut hand to much more serious events that result in significant time away from work and sometimes even more severe outcomes.
These outcomes are significantly different, but the differences in severity are not obvious when simply looking at the reported numbers. Another shortcoming: TRIRs do not give information on recordable incidents or near-misses that could have resulted in a serious injury or fatality (SIF), which are valuable indicators of a safety culture.
Lagging indicators also don't reveal how or why an incident occurred, making it hard to gauge the likelihood it could happen again. Understanding the contributing factors, root cause and actions taken are critically important. Perhaps the event prompted major changes that drastically reduced risk. But it's also possible that the contractor did nothing. It's impossible to know these answers when you're relying solely on statistics.
Benefits of Leading Indicators
Including leading indicators provides a more complete picture and allows you to identify gaps and opportunities for improvement. Aspects for evaluation include:
- Safety programs
The best safety programs identify hazards presented by each contractor’s specific scope of work and the controls that will be implemented to address identified hazards. The best programs do not regurgitate laws and regulations but rather provide clear and understandable direction for not only complying with them but, in some cases, going above and beyond to provide safe workplaces for employees.
- Safety management systems
These cultural frameworks support a contractor’s ability to execute on their safety programs and meet their company’s goals and objectives. Safety management systems include leadership engagement, employee training and development, accountability and recognition programs, inspections and hazard identification, communication, and, importantly, annual or more frequent program and performance evaluation. You can write the ideal safety program, but without robust management systems to drive execution, the programs alone are unlikely to deliver desired outcomes.
This information helps you evaluate the likelihood of future incidents, given a contractor's current safety practices.
The best companies consider leading and lagging indicators and capture real-time data in the field. Collecting and assessing safety programs, management systems, and training records are important, but we should not stop there. You need to verify that all of these are effective by performing inspections and audits throughout the lifecycle of each project. This approach delivers actionable insights that improve safety performance over time.
Elevating Contractors With Assessments
Traditional contractor selection processes relying on lagging indicators provide only surface-level evaluations, limiting your ability to mitigate risks. Your approach to prequalification shouldn't be a yes-no proposition — treat it as risk education.
Unfortunately, there is no risk-free contractor. Even "low-risk" work can involve high-risk scenarios. A comprehensive evaluation reveals exactly where risks lie — like an inadequate fall prevention program or insufficient employee training — and allows you to discuss issues with potential partners. Your goal is to cooperatively build a risk mitigation strategy with contractors when appropriate.
There may be situations where a candidate is unable to fix a problem immediately. Still, many times, you can deliver contractor success by helping them improve safety practices over time. By aligning on the risk mitigation strategy, you set clear standards and expectations. This approach allows you to work with almost any contractor by actively addressing identified risks and monitoring performance against defined action plans.
Assessing Lagging and Leading Indicators
Contractor assessment is a labor-intensive process, even without leading indicators. Evaluating the standard incident and risk statistics involves retrieving data from many sources and cross-referencing figures. Just having numbers is not enough. You must gather additional context and analyze the information to understand its meaning. When you need multiple contractors and subcontractors, time spent prequalifying contractors quickly adds up.
Leading indicators are even more complex. Manually reviewing a contractor's safety program takes multiple hours and significant mental effort. Then, you must follow up with each candidate to discuss discrepancies and expectations. This approach does not scale for larger projects.
Technology streamlines data and content analysis, delivering more robust evaluations in a fraction of the time. Contractor risk management software crunches the numbers and accounts for additional context to derive a risk score that reflects the reality of a contractor's history. AI reviews safety manuals to understand the programs and controls in place and how they compare to industry standards, allowing you to spot potential gaps that may present risk.
These actionable insights are superior to pass/fail results, empowering you to address concerns with your potential partner and collaborate on the development of a risk mitigation plan.
Ongoing safety discussions cultivate strategic partnerships. An ideal platform incorporates ongoing behavioral indicators from on-site observations to assess protocol adherence and current job site risks, surfacing trends as they occur. This insight allows you and your contractor partner to continuously improve safety throughout the project.
Just as academic performance doesn't correlate with job success, a contractor's safety record does not reveal their true risk. Leveraging AI and analytics to account for lagging and leading indicators provides a more accurate picture of a contractor's current safety profile and risk potential. This comprehensive perspective empowers you to select the right partners, foster a safer construction sight and support long-term contractor success.
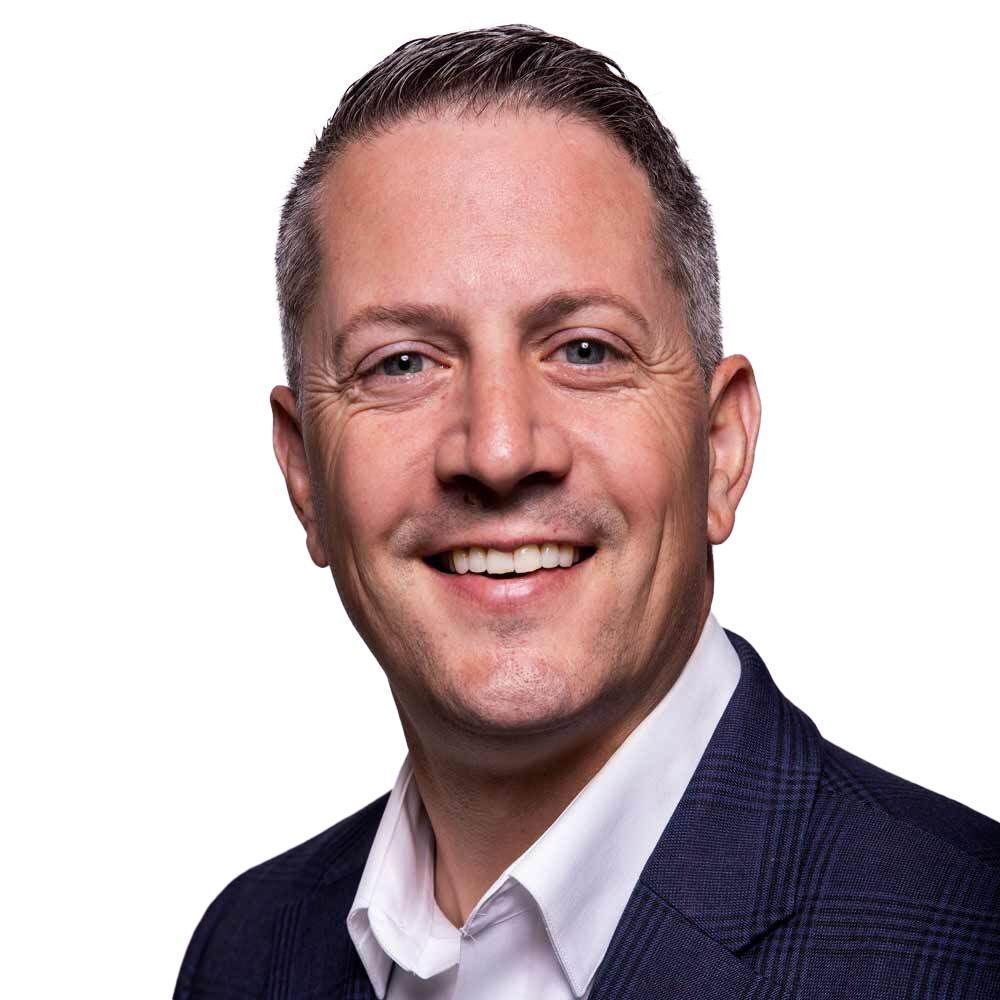
David Tibbetts, CSP
Highwire, Chief Safety Officer
David Tibbetts is a Certified Safety Professional and Chief Safety Officer at Highwire. His focus is on continued product development, client success, and customer support with the goal of helping Highwire clients deliver Contractor Success through full-lifecycle risk mitigation.