David Tibbetts, CSP

Highwire recently hosted the webinar “The Shift to SIFs: Measuring and Learning from SIF Exposures”. The engagement from the audience shed light on the growing attention around analyzing data to prevent SIFs and promote overall safety.
In this article, I am personally answering audience members’ questions that were shared during the webinar. I thank everyone who participated in advance and invite anyone with further questions to contact me directly. I’m happy to share our experiences, challenges, and successes with you along the way.
Former Managing Director at Compass Group asks:
“How do we simplify data reporting to make it easier for executives to digest?”
This is a major focus of Highwire and the SIF working group. Our goal is to create an efficient way to collect, categorize, and investigate all events with SIF potential in a consistent way. With a consistent method of data collection, we can produce simple-to-digest reports that provide executives with the visibility they need to understand emerging risks and exposures. Additionally, we want to share our experiences, challenges, and lessons learned so we can all improve together.
Sr. Principal SHE Program Manager at Genentech asks:
“How are the panelists encouraging construction teams to openly and honestly identify SIF-P and find the real root causes? How will contractors/trades be trained to identify the data and how will they enter it [into a safety management system]? Spotty or inaccurate data isn’t much better than no data.”
You absolutely raise some valid concerns about some of the challenges we see today, especially among our clients using Highwire’s inspection capability.
When it comes to inspections, we see some clients need help getting users to conduct quality inspections. In many cases, our clients are struggling with what I call “everything-is-awesome syndrome.” This is where users are hesitant to report negative findings or classify negative findings as “high-risk” or “immediately dangerous to life or health (IDLH).” One way we help combat this is through reports that measure the quality of inspections. Exploring these reports can help drive important conversations with inspectors regarding the accuracy and quality of their inspection reports. Our shared goal is to remove the mindset that documenting negative findings is a bad thing. We assert it is a good thing because it creates an opportunity to provide mentorship and improve the quality of aggregated data which helps us become better performers over time.
For incident tracking, Highwire’s upcoming SIF reporting capability grants clients the ability to review the circumstances involved in each incident and then categorize the incident as having SIF-P when applicable. Asset owners working with general contractors (GC) can override SIF categorizations produced by their GCs if they disagree with the classification. They will have the ability to upgrade or downgrade to or from SIF-P. This is an additional moment where discussion and collaboration can improve data quality.
Overcoming these challenges boils down to education and conveying the importance and value of the data we are collecting. If we approach this the right way, those barriers can be broken down and we can foster some incredible conversations—that is our hope. We will certainly experience challenges and successes along the way.
Safety Manager at Genesis AEC asks:
“SIF awareness for management is plentiful. What tools can we get to the people in the field working around the hazards? How do we get them to think about what could go wrong and ask what they’re exposing themselves to?”
Great point. We need workers to begin asking themselves these questions each day when they get to their work area.
- “What work am I performing today?”
- “What high-risk hazards will I encounter that have the potential to result in a serious injury or fatality?”
- “Do I have all of the tools and equipment I need to perform my task safely?”
- “What hazards are present in my work area?”
- “What hazards are presented by other trades or activities around me?”
While we all have some form of a daily pre-task planning process, we need to begin looking at whether or not that is focused enough on high-risk or high-energy hazards. The focus of conversations at weekly meetings—scheduled reviews, foreman, and OAC meetings—as well as daily conversations in the field should begin to have more focus on those activities with SIF-P.
Then, as we begin to aggregate meaningful data, it needs to be shared with front-line workers. We should be sharing emerging trends of types of exposures across different industries and trades as it pertains to each front-line worker’s scope of work. That data, when compiled, will facilitate many impactful conversations. We need to have immediate access to this data and share it across the industry.
Audit Manager at GSK asks:
“How do you balance encouraging the reporting of SIF exposure with the reporting of trivial near misses?”
I defer to Jason Edic’s experience at Lee Kennedy for this question:
We’re considering a ‘clearing house’ for SIF-P observations, meaning all SIF-P observations by staff members, including project managers and project executives, will have to be validated by a safety professional. When something is labeled as a SIF-P event or condition and the safety professional thinks it doesn’t meet the criteria, we have an opportunity for a teaching/learning moment with the individual who made the observation. A simple phone call could educate that individual toward the improved designation of observations in the future.
Construction Safety Director at Merck asks:
“What matrix or matrices do you use for SIF determination?”
Like many organizations, we are at the beginning of our journey. We will be using a commonly adopted matrix in the early stages which asks three questions:
1. Was there a high risk/high energy exposure?
2. Were management controls absent, ineffective, or not complied with?
3. Was the exposure allowed to continue?
Along the way, we will learn how effective this matrix is and adjust as necessary.
“What has been the collective experience in SIF reporting tracing and investigation?”
We see organizations using different terminologies and different decision processes. This is the challenge when an initiative is driven by something other than regulation. We want to create consistency and hope we can do so by sharing our experiences and our aggregated results. As we begin to aggregate data our working group will continue to meet to share our experiences that will continue to drive an improved approach.
I’d love to continue the conversation with you and continue to share our working group’s progress and lessons learned. I’d also love to hear about any successes or challenges you’ve faced.
Safety Manager at Merck & Co., Inc. asks:
“Do you find reporting/investigating near misses is helping to reduce the number of SIFs?”
As we aggregate data and learn from our experiences we will share those with you. I expect the data we collect about all events with SIF potential, including near misses, will facilitate some incredibly powerful conversations. The data will increase visibility to some significant exposures occurring on our projects today that might be getting overlooked because there is no resulting severe outcome. It will allow us to sharpen our focus to address identified risks. It will change the conversations that organizations are having internally, with their contracting partners, and with front-line workers.
Group Safety Strategy Manager at National Grid asks:
“Is there an industry-known metric or target for SIF reduction? How do you ensure learnings from SIF-P get communicated?”
This is exactly what the SIF working group is working toward. When we had a benchmark for recordable rate to measure ourselves against, we drastically reduced the average recordable rate. We expect to have this benchmark across the Highwire client base that is tracking SIF and SIF-P events. We want to share our experiences so we can all learn together.
In terms of sharing lessons learned, this information is incredibly important internally and across our network of partners. Of course, there are careful considerations to be made in terms of what gets shared and the mechanisms for sharing, but we must learn from each other so we can implement effective SIF prevention approaches.
Senior Director of EH&S at Takeda asks:
“How have you leveraged SIF data and exposures to build a predictive model?”
This is an important element of our efforts. As we begin to aggregate data and the data set grows, there is an opportunity for this data to become predictive. Clear trends will emerge, especially if we are successful in creating a consistent approach to categorizing and investigating all events with SIF-P. We can easily extract data to understand the activities that result in exposures, understand the trades experiencing the most exposures, identify common root causes, and examine many more elements. We can see this within organizations and at a larger scale across a network of partners.
Safety Director at Turner Construction asks:
“How is SIF data helping guide pre-planning and improve where staff are spending their calories?”
An excellent point here. Where are we spending our time? How are we distributing our resources so we can have the greatest impact on SIF exposure prevention?
Let’s think about it with a simple hypothetical situation involving an individual trade partner. If we could know how frequently a trade partner was involved in an event with SIF-P and we could quickly look at the common root causes, we could facilitate some really important conversations in the pre-construction phase. We would have an opportunity to help that trade partner become a better performer.
When data-driven action plans are created, we have the opportunity to focus our efforts during the course of construction. It makes planning efforts, inspections, training, toolbox talks, weekly foreman’s meetings, and check-ins more focused. The data can be used to drive organizational performance through annual self-evaluations and communications with senior leadership.
Thank you to everyone who joined us for this webinar. I am always pleased to see the safety community come together to discuss important topics like this. I invite anyone with further questions or interest to reach out.
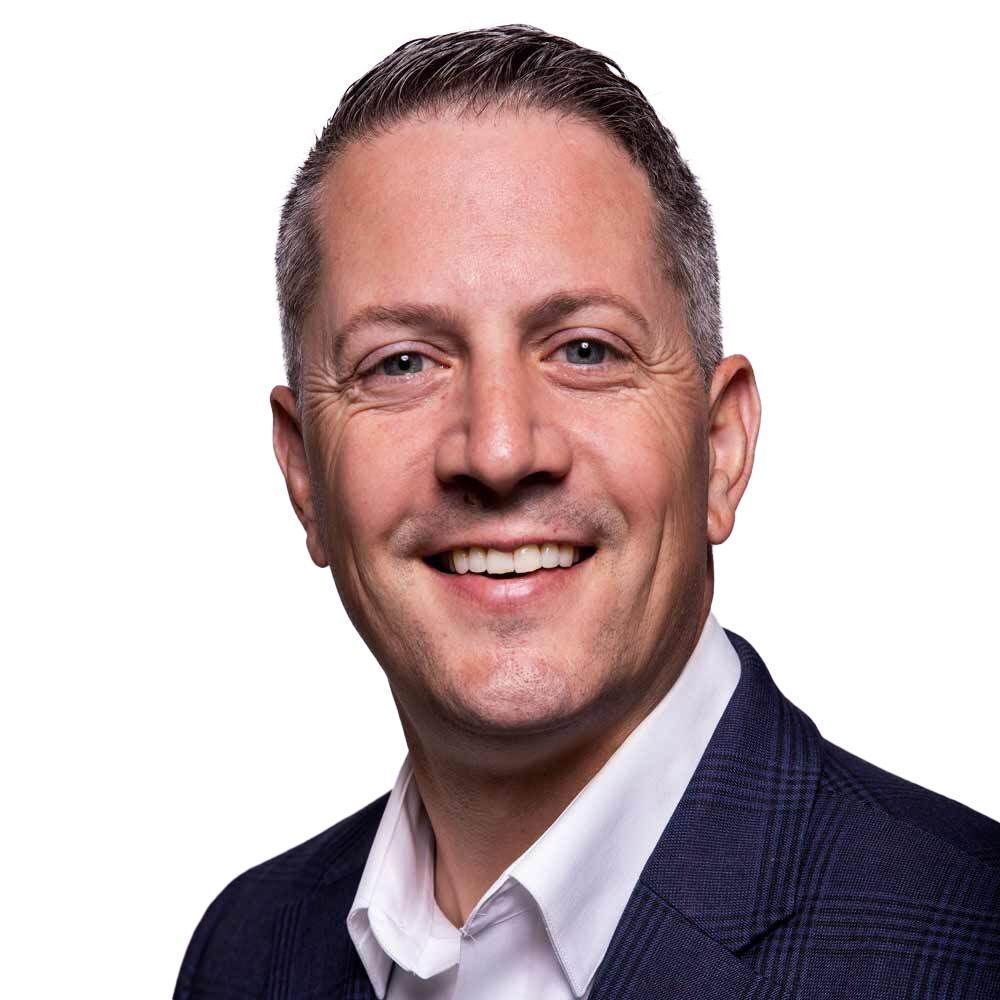
David Tibbetts, CSP
Highwire, Chief Safety Officer
David Tibbetts is a Certified Safety Professional and Chief Safety Officer at Highwire. His focus is on continued product development, client success, and customer support with the goal of helping Highwire clients deliver Contractor Success through full-lifecycle risk mitigation.