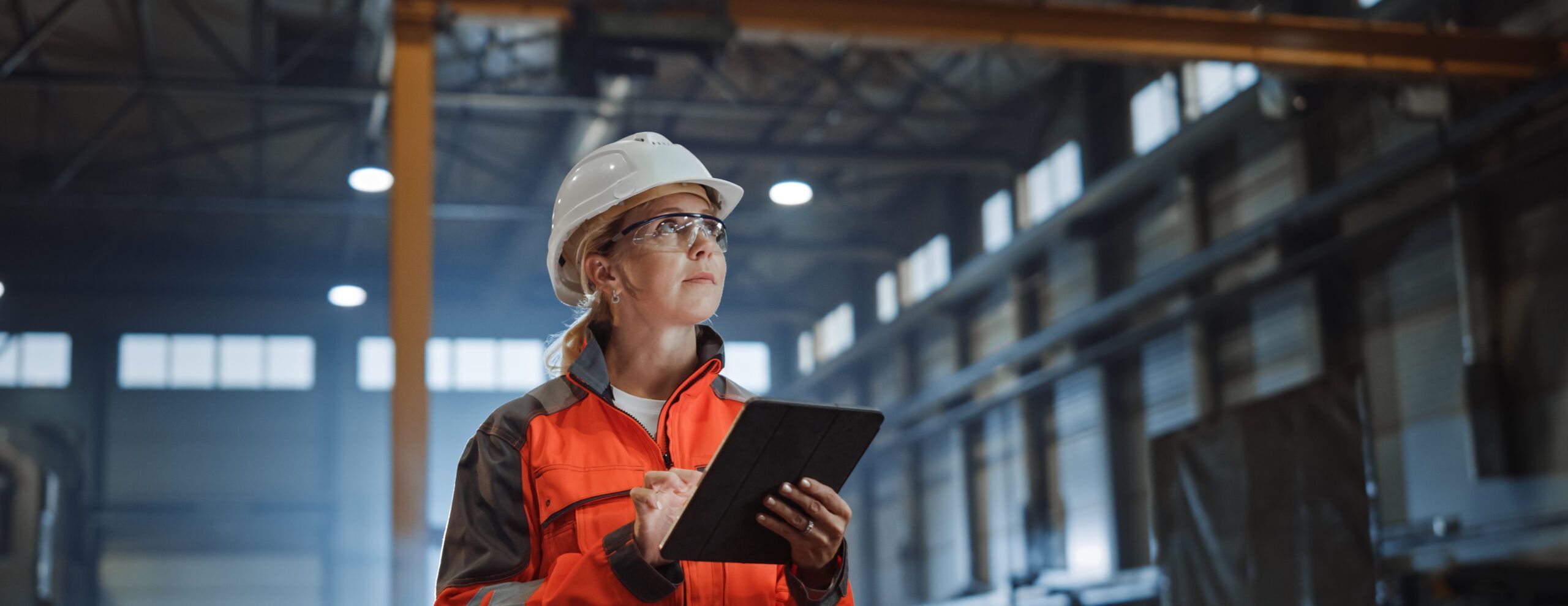
Most construction safety leaders consider flooring contractors to be relatively low-risk. The incident below, recorded by a safety inspector using Highwire, details how a “low-risk” flooring contractor suddenly created a high-risk scenario.
Wood floor workers delivered materials to the fourth-floor exterior loading zone using a scissor lift. The operator did not ensure the gate was closed before going up in the scissor lift, exposing themselves to a >40’ fall.
Fortunately, the inspector observed and corrected this IDLH exposure. His observation reflects what most high-performing organizations are beginning to understand: low-risk contractors can cause serious problems.
While work involving heights, high voltage, hazardous chemicals, and confined spaces is undoubtedly high-risk, seemingly low-risk work can also be dangerous and costly. Many owners and general contractors assume that certain contractors cannot create significant problems due to their seemingly low-risk work. However, this assumption leads to dangerous gaps in risk management since they are typically allowed to work on-site without a proper risk assessment. The highest-performing organizations have learned that these seemingly low-risk contractors can pose a substantial threat to safety and operations.
In this article, we will discuss four types of contractors that seem low-risk but can, in reality, cause incidents that lead to costly injuries, project delays, and downtime if not properly understood.
Low-Risk Tasks in High-Risk Environments
Workers must have the training they need to recognize hazards around them. Consider the following scenarios:
- A hoisting operation exposing workers to overhead loads.
- A guardrail that was removed and not put back in place.
- A falling object hazard from scaffolds or other overhead work.
- A worker recognizing and reacting to safety signage and barricades appropriately.
- Heavy equipment moving around a construction site.
These are just some examples of hazards that are present on many construction sites that workers need to be able to recognize regardless of their own scope of work.
Workers are almost always in environments and alongside teams doing work with a risk profile that can vary from their own. As a result, it is crucial for any contractor to recognize the risks of their own work and the hazards around them. Contractors performing “low-risk” work are frequently overlooked when it comes to onboarding procedures. While contractors doing millions of dollars of work may receive comprehensive onboarding tailored to the specific project, the same level of attention is often not extended to those doing a short or small piece of the project.
Contractors From Smaller Businesses
Smaller and less sophisticated companies often lack the robust safety and quality control measures that larger organizations have. As a result, they may unknowingly bring a higher level of risk to a project. It is essential to recognize the potential risks these contractors might introduce to your worksite and manage them with equal scrutiny as you would with larger and more established companies.
Lacking Ergonomic Safety Programs
While it’s easy to assume that most incidents arise from high-risk trades and activities, the reality is that risks are lurking in seemingly mundane tasks as well. Take, for example, lifting and carrying—a routine activity on construction sites. Over 50% of work-related musculoskeletal disorders stem from lifting, lowering, pushing, pulling, and carrying heavy loads, resulting in a staggering $2.5 billion in worker’s compensation costs within the construction industry.
Small injuries may seem insignificant at first, but their cumulative impact can erode profit margins over time. These recurring incidents can hinder productivity, increase medical costs, and negatively affect the overall success of a project.
Contractors with Less Experience
Experience plays a pivotal role in maintaining a safe work environment. Astonishingly, more than 40% of injuries to workers under 35 occur in their first year of employment. This fact emphasizes the need for thorough training and proper onboarding, not only for new hires but also for low-risk contractors who might need more familiarity with certain aspects of the job.
Inexperience can be a hidden landmine when it comes to low-risk contractors. Their lack of familiarity with certain high-risk scenarios and intricate processes can inadvertently create hazardous situations. While these contractors may be competent in their usual scope of work, tackling unfamiliar or complex tasks without the necessary experience can lead to costly mistakes. Consequently, it is essential to provide adequate support and supervision to ensure that low-risk contractors can navigate all aspects of the project safely and successfully, thereby minimizing potential risks and enhancing overall project performance.
Prevent Incidents, Save Millions by Vetting
The highest-performing companies have learned the value of a streamlined assessment process that encourages collaboration with all contractors, irrespective of their risk classification. Rather than treating low-risk contractors as an afterthought, they actively involve them in the risk mitigation process. This approach fosters a culture of safety, communication, and transparency, where everyone on the worksite plays a crucial role in safeguarding the project’s success. This is different from the pass/fail approach so many companies use when evaluating contractor safety. By actively engaging with contractors, understanding their strengths and limitations, and helping them improve, these companies drive project success in a multitude of ways: completing projects on time, reducing incidents and protecting their reputations.