David Tibbetts, CSP
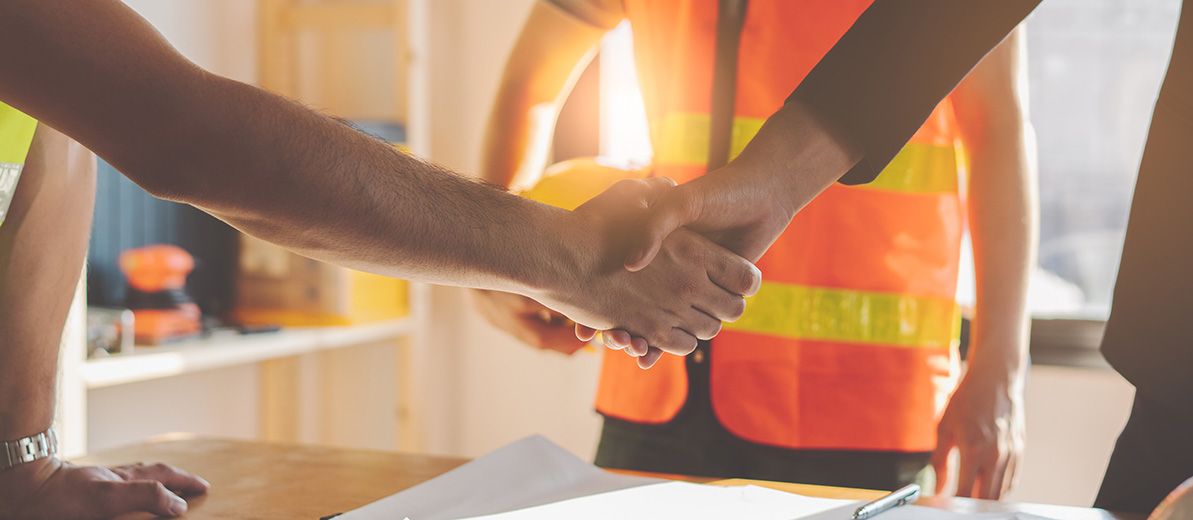
Past performance is not indicative of future success. For example, a lack of traffic tickets doesn’t mean that someone is a safe driver. The same concept is true when selecting contractors—just because a contractor has never experienced a recordable incident does not mean they are low-risk.
Many companies evaluate contractors based on past performance, including their OSHA 300A data, Total Recordable Incident Rate (TRIR), Experience Modification Rating (EMR), and Days Away, Restricted Duty or Job Transfer (DART) case rate. These lagging indicators provide valuable insight into a contractor’s qualifications but fail to show the entire picture. A contractor may have avoided a serious incident so far, but that may be a sign of luck rather than safety.
Companies must look beyond historical statistics to leading indicators in their prequalification processes, considering factors like safety programs, management systems, and culture. This information complements lagging indicators to give insight into past performance and predict future risk, supporting contractor success and generating better project outcomes.
What’s Missing In Lagging Indicators?
The industry has long viewed TRIR as a definitive indicator of a company’s overall safety performance, but research shows no correlation between recordable rates and fatalities. TRIR measurements have several shortcomings when trying to predict safety risks. First, a lack of past events does not preclude future incidents. Second, common reporting mechanisms often mask each event’s severity. A cut on the arm can look the same on paper as an injury that requires time away from work.
TRIR and other lagging indicators also fail to provide important context about how and why the incident happened, including contributing factors, root causes, and corrective actions. Was it a random and unlikely event? Was it a recurring risk that had not been addressed? Did an incident that was minor in nature have the potential to result in a serious injury or fatality (SIF-P)? Did the contractor adjust their processes in response? These details reveal a significant amount about the future risk potential.
Leading Indicators in Risk Management
Pass/fail prequalification using lagging indicators only can result in disqualifying capable contractors, a significant disadvantage amid a shortage of construction workers. Evaluating leading indicators, like safety programs and safety management systems, enables a more comprehensive risk assessment and highlights areas for improvement.
A contractor’s safety program should go beyond restating rules and regulations to provide clear directions, not just for compliance, but for ensuring a high level of execution that protects workers. Ideally, these programs exceed minimum standards, identify hazards presented by each contractor’s specific scope of work, and outline targeted measures to mitigate identified hazards.
Safety management systems drive safety program execution. Without these cultural frameworks, programs alone are unlikely to deliver the desired outcomes. Elements of an effective system include:
- Leadership commitment and engagement
- Employee training and development
- Accountability and recognition programs
- Inspections and hazard identification
- Frequent program and performance evaluation
- Incentive and recognition programs
Insight into safety management systems allows safety and procurement leaders to assess the probability of future events. Research revealed that having more safety management systems was linked to lower rates of recordable incidents.
Capturing real-time data from the field provides another mechanism for understanding contractor risk. On-site inspections and audits allow project teams to evaluate performance and identify ways to enhance safety over time.
Gathering data beyond historical statistics turns prequalification processes into opportunities for improvement. Companies can pinpoint risks and work with potential partners to set expectations and create a mitigation strategy. This type of collaboration can deliver successful outcomes allowing companies to work with almost any contractor.
Building A Comprehensive Contractor Safety Evaluation Process
Facilities management and operations teams know the challenges involved in collecting prequalification data from contractors. They must collect statistics from multiple sources, cross-reference figures, gather additional context, and analyze all the data.
In light of this workload, adding the evaluation of leading indicators can seem daunting. Manually examining a contractor’s safety protocols and following up with individual contractors is time-intensive and mentally demanding. It’s not feasible to execute this process by hand.
Specialized contractor risk management software expedites prequalification by gathering and processing data while accounting for additional context. These platforms deliver a comprehensive risk score that accurately reflects a contractor’s safety posture in a fraction of the time it would take a human. Artificial intelligence (AI) can analyze safety programs and management systems to identify potential risks, such as an inadequate fall prevention program.
With this insight, facilities management and operations teams can approach potential contractors to address concerns through a collaborative risk mitigation strategy. These discussions create a shared goal and enhance strategic partnerships.
Sophisticated teams use a contractor risk management solution to incorporate on-site observations to continuously evaluate performance and identify emerging trends and risks. This information empowers contractors and field teams to improve safety practices over time.
The landscape and approach to contractor prequalification are evolving. Combining lagging and leading indicators is important in understanding a contractor’s safety profile and risk potential. Technological advances make comprehensive analysis accessible to companies of all sizes, empowering them to select the ideal partners, enhance worker safety, and support contractor success.
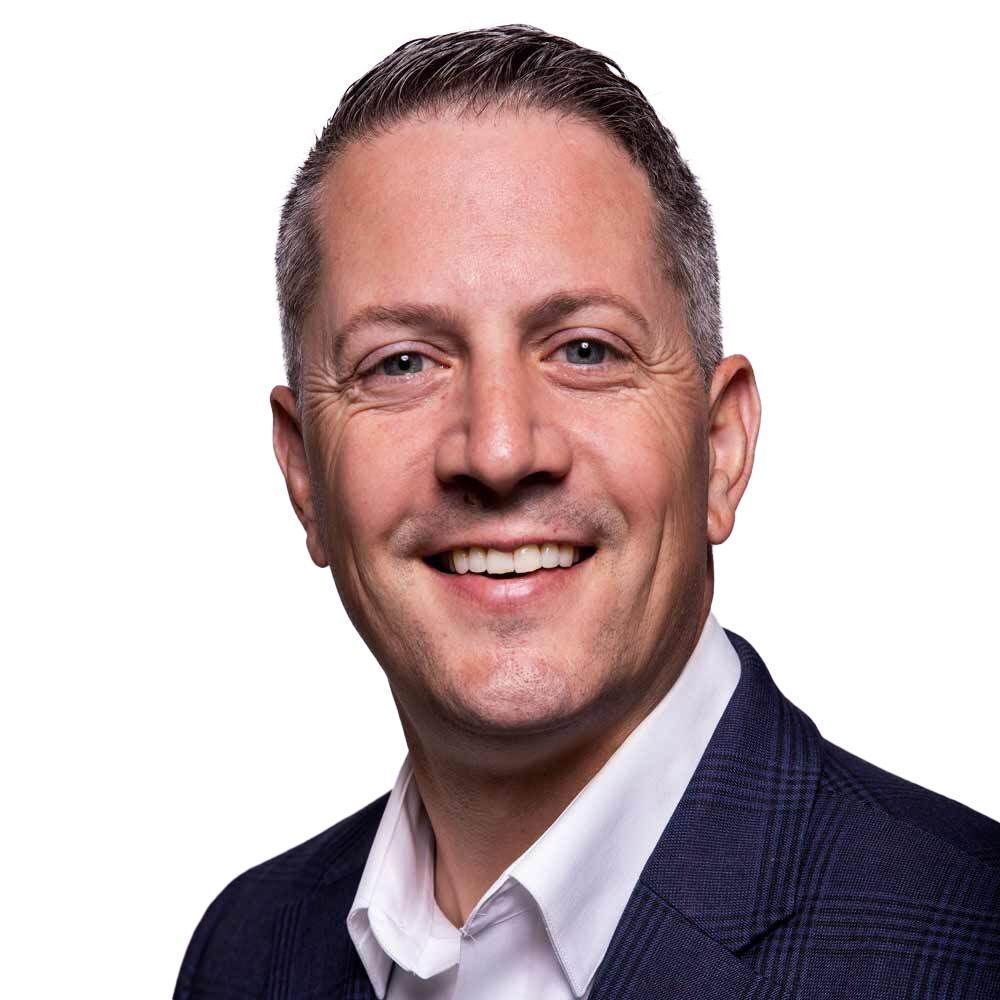
David Tibbetts, CSP
Highwire, Chief Safety Officer
David Tibbetts is a Certified Safety Professional and Chief Safety Officer at Highwire. His focus is on continued product development, client success, and customer support with the goal of helping Highwire clients deliver Contractor Success through full-lifecycle risk mitigation.