David Tibbetts, CSP
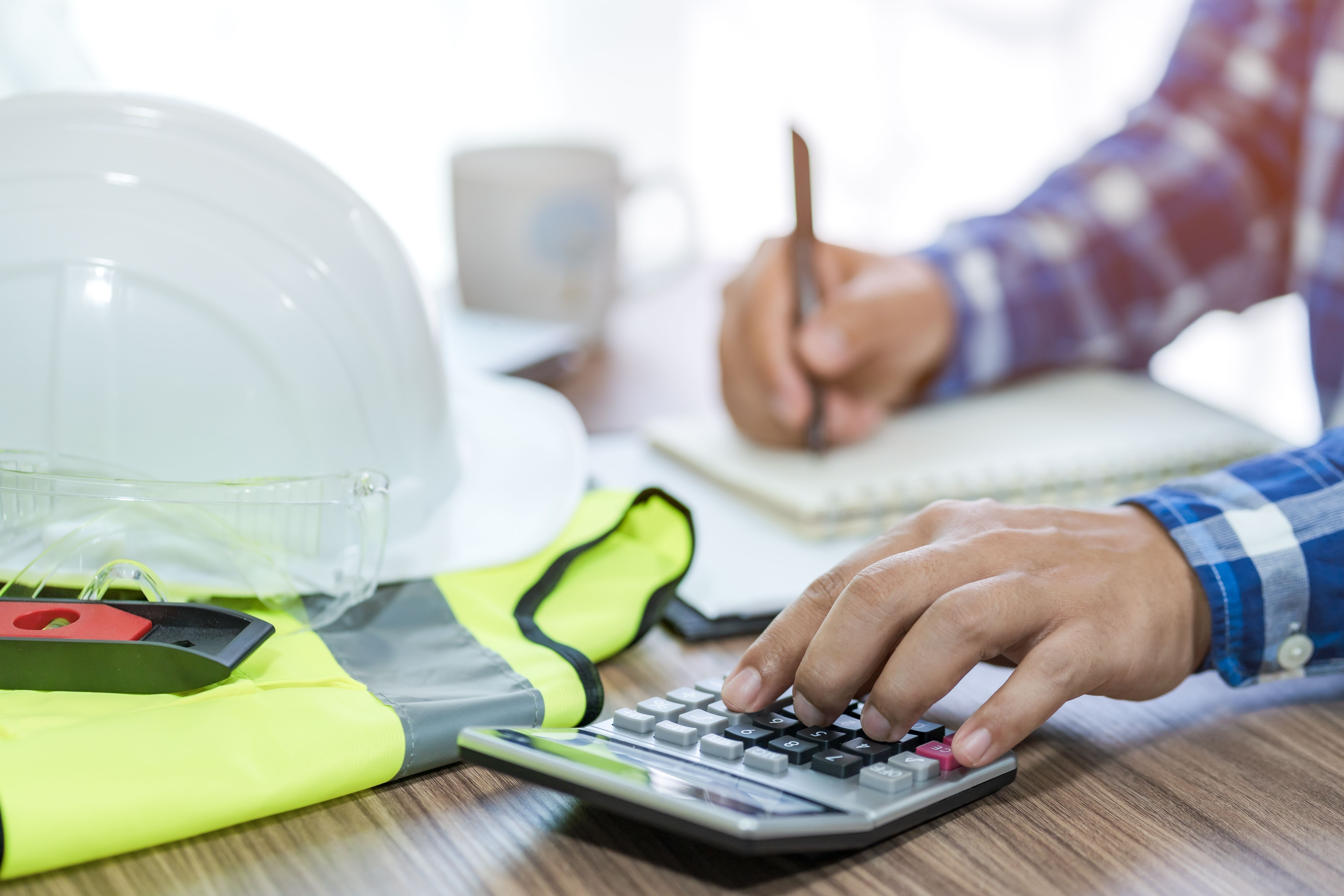
In 2023, private industry employers reported 2.6 million nonfatal workplace injuries and illnesses. That number is a stark reminder of how critical workplace safety is, especially in high-risk industries like construction and manufacturing. But how do organizations measure how safe they really are? One common measure is Total Recordable Incident Rate (TRIR). This metric gives companies a way to track workplace injuries and compare safety performance against industry benchmarks.
The problem is that TRIR doesn’t always tell the full story. While it’s a standard benchmark used by OSHA, it focuses only on past incidents. A high TRIR can result in more attention from OSHA, increased insurance premiums as EMR’s rise, and damage to a company’s reputation. At the same time, a TRIR that is better than industry benchmarks is not always indicative of a strong safety culture.
In this article, we’ll explain what TRIR is, how to calculate it, andits limitations. More importantly, we’ll show you how to move beyond TRIR and take a smarter, more proactive approach to managing workplace safety.
What is TRIR?
TRIR (Total Recordable Incident Rate) is a standardized metric that tracks workplace injuries and illnesses. It reflects the number of OSHA recordable incidents per 100 full-time employees in a given year. It’s used primarily in industries with higher safety risks, like construction, manufacturing, and energy, where maintaining safety is critical. Here’s how organizations and regulators use TRIR:
- Benchmarking: TRIR allows companies to compare their safety performance with others in their industry.
- Regulatory Scrutiny: OSHA may conduct more frequent inspections on businesses with higher-than-average incident rates.
- Risk Assessment: Asset owners and general contractors commonly use TRIR when assessing the potential risks presented by contractors bidding and working on their projects. Contractors with elevated TRIR’s often face more scrutiny during the bid process. .
While TRIR provides a snapshot of previous safety performance, it’s important to know how to calculate it correctly to ensure accurate benchmarking. Let’s break down the formula and how to apply it.
How to Calculate TRIR
The formula for calculating Total Recordable Incident Rate (TRIR) is:
TRIR = (Number of Recordable Incidents × 200,000) ÷ Total Hours Worked in a Year
Why 200,000? This number represents the total hours worked by 100 full-time employees, assuming a 40-hour work week for 50 weeks. It provides a consistent way to compare safety performance across companies of different sizes.
Key Points to Remember
- Exclude vacation, sick leave, and other non-working hours from the total.
- Count only incidents that meet OSHA’s recordability criteria
Example Calculation
Imagine your company had 5 recordable incidents last year, with employees working a total of 250,000 hours:
TRIR = (5 × 200,000) ÷ 250,000
TRIR = 1,000,000 ÷ 250,000 = 4.0
In this case, your TRIR is 4.0, meaning your company experienced four recordable incidents for every 100 full-time employees over the past year.
Now that you know how to calculate TRIR, understanding what the number actually means is key. TRIR provides useful insights, but its significance depends on how you interpret and apply it within the broader context of your industry and company size.
Putting TRIR in Context
A high TRIR may signal serious safety concerns, while a low TRIR often suggests an effective safety management system. However, company size can significantly affect the impact of a single incident. Smaller establishments may see large TRIR fluctuations from just one event, making it essential to consider total hours worked when reviewing a contractor’s rates.
To help with these comparisons, the Bureau of Labor Statistics (BLS) provides incident rate data categorized by industry, and average TRIRs can vary widely. For example, in 2023, framing contractors and siding contractors had TRIRs of 5.5 and 5.8 respectively while painters and tile and terrazzo contractors had rates of 1.6 and 1.5.
TRIR serves as a valuable tool for benchmarking safety performance. If your company’s TRIR is higher than the industry average, it may indicate a need for targeted safety interventions. Conversely, a lower-than-average TRIR can reflect a strong safety program. However, keep in mind that TRIR offers only a partial view of safety performance. It doesn’t capture near misses, safety observations, or events with the potential to result in a serious injury or fatality or SIF.
Interpreting your TRIR accurately starts with ensuring you’re including the right incidents in your records. Not every workplace injury or illness qualifies as recordable, so it’s crucial to know what OSHA considers a recordable incident.
What Qualifies as a Recordable Incident?
According to OSHA, a recordable incident is a work-related injury or illness that meets specific criteria for severity and treatment. Recordable incidents must meet at least one of the following conditions:
- Any work-related fatality
- Any work-related injury or illness that results in loss of consciousness, days away from work, restricted work, or transfer to another job
- Any work-related injury or illness requiring medical treatment beyond first aid
- Any work-related diagnosed case of cancer, chronic irreversible diseases, fractured or cracked bones or teeth, and punctured eardrums
- There are also special recording criteria for work-related cases involving: needlesticks and sharps injuries; medical removal; hearing loss; and tuberculosis
Examples of Recordable Incidents
Understanding recordable incidents is easier with practical examples:
- Loss of consciousness: If an employee faints or loses consciousness due to a work-related injury, it must be recorded.
- Lacerations requiring stitches: A deep cut needing sutures involves medical treatment beyond first aid and qualifies as recordable.
- Restricted work duties: If a back injury limits an employee’s ability to perform just one of their normal tasks for several days, this is a recordable incident.
However, not every workplace mishap is recordable. For instance, if an employee receives basic first aid, like a bandage for a minor scrape, and continues work without restriction, it doesn’t count as a recordable incident. Knowing the difference is key to maintaining accurate records and avoiding unnecessary reporting.
Clear recordkeeping is essential for compliance and ensures your TRIR accurately reflects your safety performance. But even with the right data, TRIR has its limitations. Let’s explore why this metric doesn’t always tell the whole story.
The Limitations of TRIR
While Total Recordable Incident Rate (TRIR) is a widely used metric, it has limitations that are important tounderstand. Knowing these weaknesses can help you avoid relying too heavily on a single data point.
- It’s a Lagging Indicator: TRIR focuses on incidents that have already happened. It doesn’t provide real-time insights into current or emerging risks. This makes it less useful for predicting future incidents or identifying potential hazards before they occur.
- Misleading Data: A low TRIR does not necessarily mean low risk. Similarly, an elevated TRIR does not always indicate high risk. Understanding how to use TRIR in combination with other metrics and understanding what questions to ask when TRIR is elevated is critical. Companies with an elevated TRIR may have taken several steps to improve performance and recordable injuries may have been minor in nature. Companies with a low TRIR may not have a high frequency of injuries but injuries might be severe in nature.
- It Doesn’t Reflect Safety Culture: TRIR only measures recordable incidents. It overlooks near misses, events with the potential to result in a Serious Injury or Fatality (SIFs), employee engagement, and other proactive efforts to prevent injuries. A workplace might have a low TRIR but still face significant risks if it ignores underlying issues like unsafe conditions and unsafe behaviors, poor communication, or unreported hazards.
- Risk of Misuse: Relying solely on TRIR can lead to unintended consequences. Companies that prioritize keeping TRIR low may discourage employees from reporting incidents or near misses, ultimately harming safety efforts. A well-rounded approach should include other metrics and qualitative feedback.
Relying on TRIR as the sole measure of safety performance can be misleading. TRIR only captures recordable incidents, offering a narrow snapshot of workplace safety.
How TRIR Can Overemphasize Minor Incidents
While TRIR is an important safety metric, it can sometimes place too much focus on incidents that are relatively minor. Because OSHA defines a recordable incident based on medical treatment beyond first aid, certain events, while not necessarily reflective of a hazardous work environment, can still impact your TRIR.
Here are some examples of relatively minor incidents that meet the definition of a recordable injury:
- Bee Stings or Insect Bites: A sting becomes recordable if an employee receives prescription medication or medical treatment beyond first aid, even if it happened in a low-risk environment like an office parking lot.
- Small Cuts Requiring Stitches: A minor cut that could have been treated with a bandage but instead required stitches must be recorded, even if it didn’t cause lost work time.
- Prescription-Strength OTC Medications: If a doctor prescribes an over-the-counter (OTC) medication at a higher dosage, such as 800 mg of ibuprofen instead of advising the employee to take a standard 200 mg tablet, the case becomes recordable. Even if the injury is a mild sprain or strain, it inflates TRIR without reflecting a significant safety issue
- Foreign Objects in the Eye: A tiny speck of debris that requires removal by a doctor is considered recordable, regardless of whether it caused any real harm.
These types of incidents highlight why TRIR alone doesn’t always reflect the overall safety of a workplace. While preventing all injuries is the goal, a single bee sting or minor muscle strain shouldn't overshadow bigger safety risks that may be going unnoticed.
Understanding the True Severity of a Recordable Incident
Looking at your TRIR alone won’t tell you which incidents were serious and which were minor. The OSHA 300A summary only provides a total count of recordable incidents. It doesn’t distinguish between a severe injury and a minor one that just happened to meet OSHA’s criteria. To truly understand workplace safety risks, you need to dig deeper into OSHA 300 logs and analyze the details of each recordable case.
This process isn’t simple. It requires reviewing each incident’s cause, severity, and impact rather than just counting how many occurred. Here’s why that matters:
- A TRIR of 4.0 could mean very different things. It might indicate several serious injuries requiring hospitalization, or it could be a handful of minor cases, like an employee receiving prescription-strength ibuprofen for a mild strain.
- The 300A report lacks context. It only gives totals, offering no insight into which injuries resulted in significant lost workdays or permanent impairment.
- The OSHA 300 log provides the details you need. This is where you’ll find what actually happened, including the type of injury, the affected body part, the medical treatment given, and whether the employee had to miss work or transfer jobs.
Not all recordable incidents reflect a company's actual safety performance. TRIR calculations don’t account for who was responsible for an incident, only that it happened. This can create misleading conclusions, especially when an event occurs due to factors beyond a company’s control.
For example, imagine a construction site where a crane operated by one company collapses, killing two workers from a different company on-site. Under OSHA’s recordkeeping rules, the employer of the deceased workers, not the company operating the crane, must record the fatalities on their OSHA 300 log. Even though they had no involvement in the incident, their TRIR now reflects two workplace fatalities.
Analyzing the OSHA 300 log is time-consuming but critical. Without it, you’re working with incomplete data, which could lead to poor safety decisions. A high TRIR might look alarming on paper, but without reviewing the logs, you won’t know if those incidents reflect true safety hazards or just minor medical treatments that inflated the number. If you want an accurate picture of workplace safety, you must go beyond the 300A summary and examine your full OSHA 300 logs.
How to Improve Workplace Safety Beyond TRIR
To build a safer workplace, it’s essential to go beyond lagging indicators like TRIR. Focusing on proactive strategies, like tracking leading indicators and fostering a strong safety culture, can make a significant difference.
Track Leading Indicators
Leading indicators measure proactive safety efforts rather than just outcomes. Examples include:
- Near-miss reports
- Safety observations
- SIF-potential events
- Employee participation in training programs
By monitoring these data points, you can detect early signs of potential problems and address them before incidents occur.
Invest in Real-Time Insights
Technology can transform how you manage safety. Real-time data collection tools, such as digital incident reporting systems or wearable safety devices, help identify trends and risks as they emerge. With faster access to information, you can respond more effectively and prevent small issues from escalating.
Implement Comprehensive Contractor Management
Contractors present risk and bring added complexity to workplace safety. Ensure they meet your safety standards through:
- Prequalification assessments to understand their safety performance history and capabilities.
- Regular safety audits to monitor performance and identify emerging risks.
Holding contractors accountable promotes consistency and reduces risks across your operations.
Build a Strong Safety Culture
A strong safety culture driven by company leadership is critical to reducing incidents. Foster an environment where employees feel comfortable reporting hazards and near misses without fear of reprisal. Transparency and open communication create trust and encourage participation in safety initiatives. Involve employees at all levels in safety discussions, reinforce and recognize positive behaviors, and provide continuous feedback. This not only improves engagement but also strengthens your overall safety program.
While these strategies can transform your safety program, having the right tools and technology makes it easier to implement them. Highwire can help.
How Highwire Can Help You Move Beyond TRIR
Highwire empowers organizations to move beyond TRIR by offering the tools and insights needed for proactive risk management and continuous safety improvement. Here’s how:
- Real-Time Tracking of Leading Indicators: Highwire captures and analyzes key safety data, like near misses and safety observations, giving you a full view of your proactive safety efforts. Our real-time dashboards help you spot trends and act before incidents occur.
- Instant Access to Real-Time Insights: With Highwire, you get real-time access to safety data across your organization. Identify risks as they emerge, monitor contractor performance, and make data-driven decisions that improve safety outcomes.
- Comprehensive Contractor Management: Highwire ensures every contractor you work with meets your safety standards. Our platform supports prequalification assessments, ongoing safety audits, and performance tracking to promote accountability and reduce risk across your projects.
- Support for Building a Strong Safety Culture: Highwire helps foster a safety culture built on trust and accountability. Our tools encourage transparent hazard reporting, track near misses, and recognize positive safety behaviors, boosting engagement at every level.
Ready to move beyond basic compliance and build a safer workplace? Request a demo today to see how Highwire can help you lead the way in proactive safety management.
Frequently Asked Questions (FAQ)
- How is TRIR calculated? TRIR is calculated by multiplying the number of OSHA-recordable incidents by 200,000, then dividing that total by the number of hours worked by all employees. This standardizes the rate for easy comparison across companies and industries.
- Why is TRIR divided by 200,000? The 200,000 figure represents the total hours 100 full-time employees would work in one year, assuming each works 40 hours per week for 50 weeks. This ensures consistency when comparing safety performance between organizations.
- What is a good TRIR? A good TRIR varies depending on the industry. High-risk sectors like construction or manufacturing often have higher average TRIRs, while low-risk industries typically have lower rates.
- What is the TRIR calculation? The formula for TRIR is: (Number of Recordable Incidents × 200,000) / Total Hours Worked. This gives the number of recordable incidents per 100 full-time employees in a year.
- What is the difference between EMR and TRIR? EMR (Experience Modification Rate) is an insurance metric used to determine workers' compensation premiums based on past claims history. TRIR, on the other hand, measures the frequency of workplace incidents and helps monitor safety performance over time.
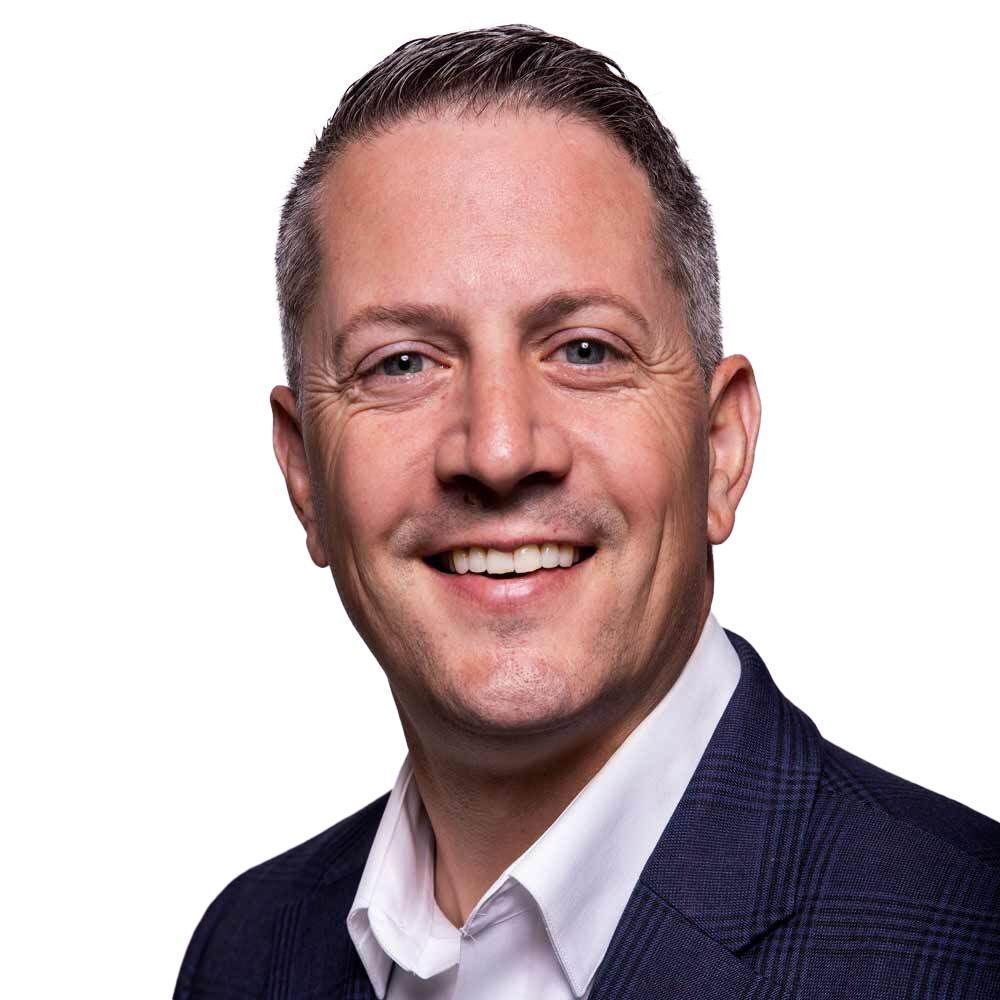
David Tibbetts, CSP
Highwire, Chief Safety Officer
David Tibbetts is a Certified Safety Professional and Chief Safety Officer at Highwire. His focus is on continued product development, client success, and customer support with the goal of helping Highwire clients deliver Contractor Success through full-lifecycle risk mitigation.